
#Combined heat and power simulation on aspen hysys plus
Furthermore, the model of pyrolysis was created using Aspen Plus software. During the experiment, gaseous products were analysed to determine a change in the gas composition with increasing temperature. Pyrolysis experiments of waste spruce sawdust were carried out. Pyrolysis is an important phenomenon in thermal treatment of wood, therefore, the successful modelling of pyrolysis to predict the rate of volatile evolution is also of great importance. This study is aimed at obtaining a support tool for optimal solutions assessment of different gasification plant configurations, under different input data sets.Ībstract Over the past decades, a great deal of experimental work has been carried out on the development of pyrolysis processes for wood and waste materials.
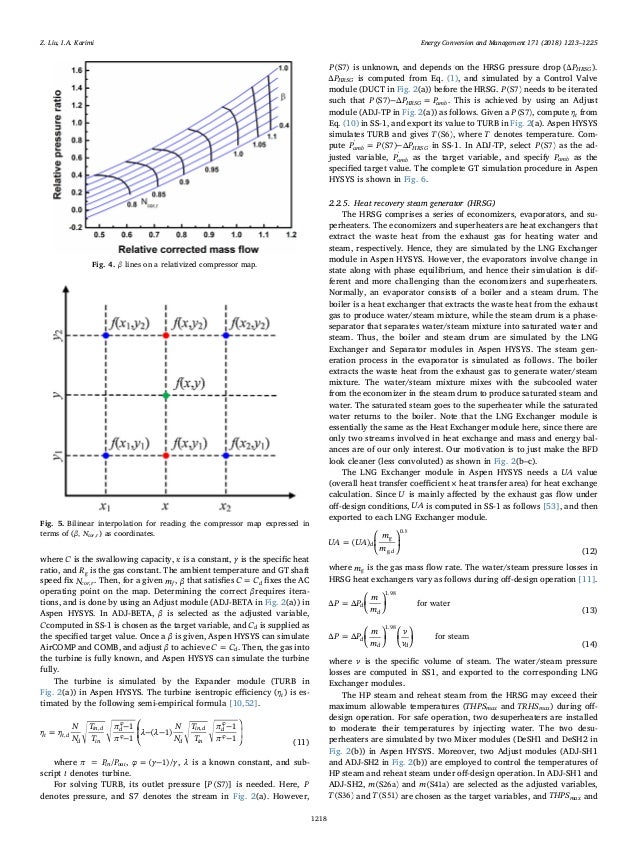
Predicted results of clean gas composition and generated power present a good agreement with industrial data. Parts of it have been developed in Matlab, which is mainly used for artificial neural network (ANN) training and parameters estimation. A process simulation was undertaken, using Aspen Plus and the engineering equation solver (EES).The The model has been developed using Aspen Hysys® and Aspen Plus®. Some thermodynamic inefficiencies were found to shift from the gas turbine to the steam cycle and redox system, while the net efficiency remained almost the same. Thus far, the SGR process and the HGD unit are not commercially available. Heat integration is central to the design. This work presents a in the proposed process, diluted hydrogen is combusted in a gas turbine.
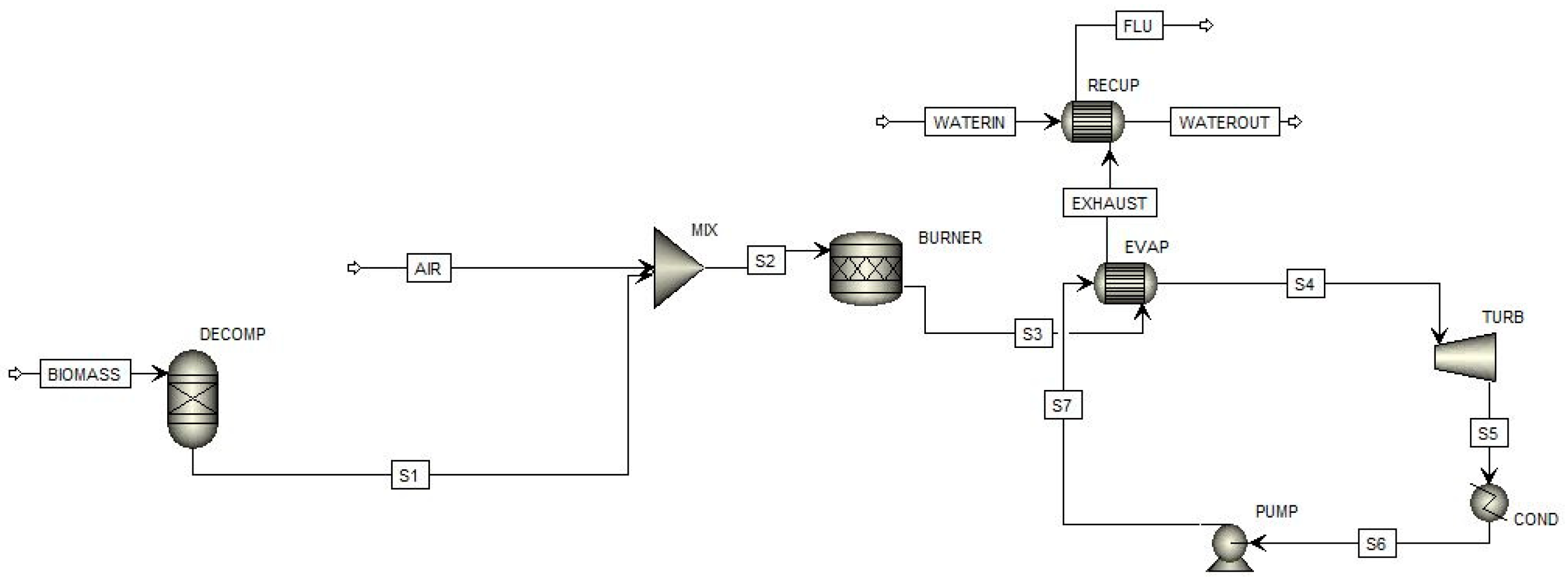
IGCC, abbreviation of Integrated Gasification Combined Cycle, is one of the primary designs for the power-generation market from coal-gasification. As a result, coal-fired power plant remains to be a fundamental element of the world's energy supply. Among all those energy resources, coal is readily available all over the world and has risen only moderately in price compared with other fuel sources. The calculations show that when using a condensing boiler, a triple energy effect is achieved: the physical heat of the flue gases is used the latent heat of vaporization released during condensation is used the condensate released from the flue gases is used.Įlectricity is an indispensable amenity in present society. Using the Aspen Plus computer program, the condensation unit circuit was simulated at the PTVM-100 boiler unit with the specification of the optimal operating parameters of material flows and heat exchange equipment. The boiler furnace is modeled as a Gibbs reactor, which calculates the chemical and thermodynamic equilibrium by minimizing the difference in the Gibbs energy of the products and the starting materials. The configuration of tees (mixers) is carried out by setting the costs or fractions of two flows entering or leaving the element. In this scheme, there are tees, heat exchangers and a reactor (boiler furnace). To analyze the main energy indicators of the condensing unit and optimize its operating modes, a priority scheme was simulated in Aspen Plus.
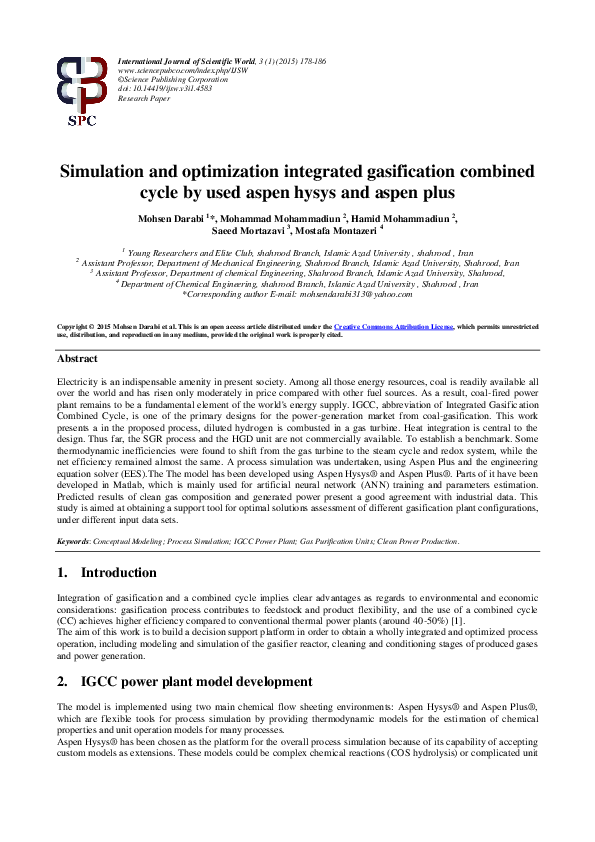
It has been established that in boiler units operating on natural gas, the only way to significantly improve the use of fuel is to deeply cool the combustion products to a temperature at which it is possible to condense the maximum possible portion of the fumes contained in the gases. The article discusses the scheme of deep utilization of the heat of flue gases.
